Product Category
Container sealing requirements for liquefied gas storage tanks
Date: Jan 14, 2020
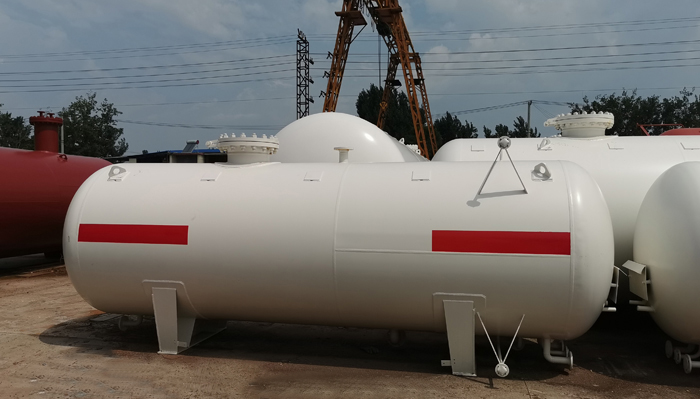
Friends who are concerned about LPG storage tank storage tanks will notice that the seals of pressure vessels are usually designed to be cylindrical, which can better withstand greater pressure. liquefied petroleum gas storage tanks are usually made of ferrous metal, which facilitates sealing between materials.
The size and shape of the seal between the lead and the sealed container directly affect the sealing effect. The larger the diameter of the end face of the sealing mouth, the greater the total pressure on the sealing material, and the greater the shear force between the sealing material and the container wall. If the seal is too small, it will affect the placement of wires and components.
In addition, in order to reduce the pressure on the sealing material, the sealing mouth is designed to be conical, and a non-metal gasket is placed near one end of the container to facilitate the molding of the sealing material during sealing. After the mold is made, the wall of the cylinder to be poured becomes rough and then immersed in acetone. One end of the mold is sealed with a sealing material, and the other end is connected to the water outlet of the hydraulic press. The choice of materials is cast epoxy sealant, polyurethane sealant and polysulfide.
According to analysis, in order for the sealing system to withstand higher pressure, the material itself must have good water resistance; sufficient compression and strength; no shrinkage or certain toughness during the curing process. We have developed an improvement plan for existing materials: using polysulfides to modify epoxy resins; combining and using epoxy resins and silicone sealants; coating a layer of epoxy structural adhesive on the wall of the seal to increase The adhesion of the transition layer to the metal interface.
When designing a liquefied petroleum gas storage tank seal, the smaller the cross-sectional area of the pouring opening, the better the sealing performance. Due to the shrinkage of the sealant during curing, the bonding strength between the sealant and the wall material will be greatly reduced. Therefore, it is necessary to roughen the joint surface of the cylinder wall. At the same time, some modifications must be made to the adhesive to increase its toughness so that it can maintain close contact with the adhered surface when subjected to pressure.
The size and shape of the seal between the lead and the sealed container directly affect the sealing effect. The larger the diameter of the end face of the sealing mouth, the greater the total pressure on the sealing material, and the greater the shear force between the sealing material and the container wall. If the seal is too small, it will affect the placement of wires and components.
In addition, in order to reduce the pressure on the sealing material, the sealing mouth is designed to be conical, and a non-metal gasket is placed near one end of the container to facilitate the molding of the sealing material during sealing. After the mold is made, the wall of the cylinder to be poured becomes rough and then immersed in acetone. One end of the mold is sealed with a sealing material, and the other end is connected to the water outlet of the hydraulic press. The choice of materials is cast epoxy sealant, polyurethane sealant and polysulfide.
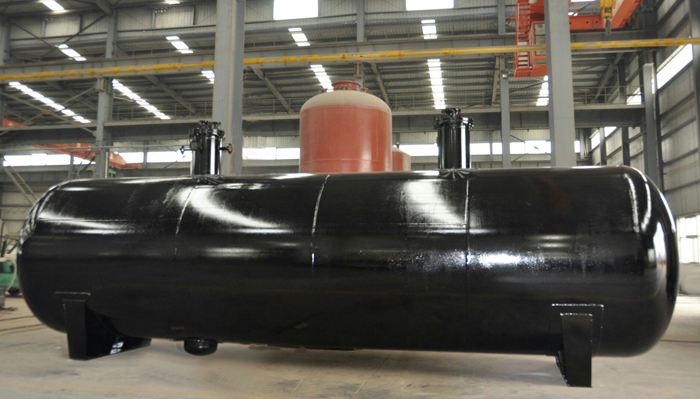
When designing a liquefied petroleum gas storage tank seal, the smaller the cross-sectional area of the pouring opening, the better the sealing performance. Due to the shrinkage of the sealant during curing, the bonding strength between the sealant and the wall material will be greatly reduced. Therefore, it is necessary to roughen the joint surface of the cylinder wall. At the same time, some modifications must be made to the adhesive to increase its toughness so that it can maintain close contact with the adhered surface when subjected to pressure.
Last article:
Next article:
Send Your Inquiry
We not only provide a good product, but also provide high quality service. If you are interested in our products,
you can contact us in the following ways.
you can contact us in the following ways.