Product Category
Anticorrosion method of oil tank
Date: Jan 15, 2020
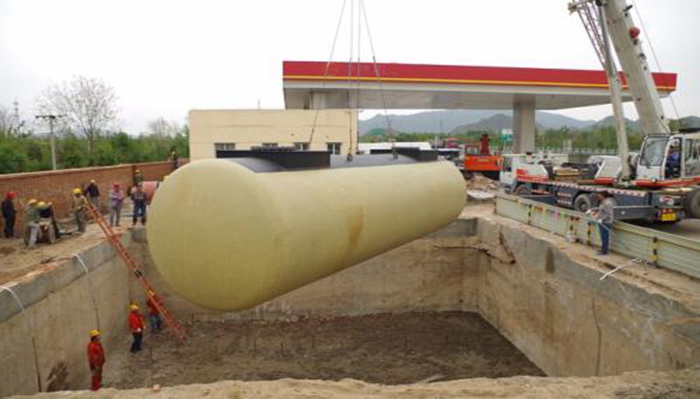
1、 Anticorrosion of inner wall of oil tank
There are the following types of corrosion on the inner wall of the oil tank: concentration corrosion, which mainly occurs below the liquid level of the inner wall of the oil tank, due to the concentration difference of oxygen. Galvanic corrosion (electrochemical corrosion), which is the most important and harmful corrosion, mainly occurs at the bottom, wall and top of the tank. The anode area and cathode area of electrochemical corrosion are formed due to the potential difference caused by the micro heterogeneity of the material itself, while the main reason for electrochemical corrosion is the water, salt and acid contained in the oil. Corrosion caused by sulfate reducing bacteria and other bacteria mainly occurs at the bottom of the tank. Friction corrosion mainly occurs in floating expansion part of floating roof tank.
The anti-static and anti-corrosion coating applied in the tank of petroleum products is quite different from other industrial coatings. It must meet two requirements: first, in addition to anti-static, it must have excellent anti rust ability for steel; the inner coating of the tank is immersed in the state of petroleum products, and the immersed state is more conducive to the penetration of corrosive medium through the paint film and corrosion of steel than the atmospheric environment; second, It must be resistant to immersion of petroleum products for a long time, and do not pollute or cause deterioration of petroleum products.
The primer is composed of modified epoxy resin, zinc powder and high-performance curing agent. It is corrosion-resistant based on the principle of sacrificial anode. The iron is not corroded in exchange for the electrons released by zinc powder. The primer has fast drying, excellent impermeability, excellent corrosion-resistant performance and strong adhesion. It is suitable for tank farm environment. The top coat of the scheme is composed of special resin, special pigment and conductive filler, which has excellent antistatic and anticorrosive ability.
2、 Anticorrosion of outer wall of fuel tank
The outer wall of fuel tank is in chemical atmospheric environment, and the main corrosion type is primary battery corrosion, which is lighter than that in the tank, but requires outstanding weather resistance. In addition, the environmental temperature of the anti-corrosion oil tank may have an adverse impact on the product. For example, the high temperature in summer is not conducive to the storage of low boiling point oil products, so measures of heat insulation and temperature reduction must be taken to reduce oil loss and ensure production safety.
The recommended anti-corrosion coating scheme for the outer wall of oil tank is: epoxy Iron Red Antirust Primer (brush or spray 2-3 layers, thickness 80-100 μ m) + epoxy micaceous iron intermediate coating (brush or spray 2-3 layers, thickness 100-120 μ m) + tank thermal insulation and anti-corrosion finish (brush or spray 2-3 layers, thickness 80-100 μ m). For the sandblasted surface of pressure vessel, epoxy zinc rich primer (brush or spray 2-3 layers, thickness 80-100 μ m) can be used Degree 80-100 μ m) to enhance the anti-corrosion effect. Epoxy micaceous iron midcoat has a good shielding effect, and can play a lasting protective role in long-term anti-corrosion engineering. The tank insulation coating can reduce the oil temperature (compared with that when the coating is not applied) by 7-10 ℃ in summer and high temperature season, and has excellent weather resistance and anti-corrosion decorative ability, and the paint film is resistant to spray water erosion.
There are the following types of corrosion on the inner wall of the oil tank: concentration corrosion, which mainly occurs below the liquid level of the inner wall of the oil tank, due to the concentration difference of oxygen. Galvanic corrosion (electrochemical corrosion), which is the most important and harmful corrosion, mainly occurs at the bottom, wall and top of the tank. The anode area and cathode area of electrochemical corrosion are formed due to the potential difference caused by the micro heterogeneity of the material itself, while the main reason for electrochemical corrosion is the water, salt and acid contained in the oil. Corrosion caused by sulfate reducing bacteria and other bacteria mainly occurs at the bottom of the tank. Friction corrosion mainly occurs in floating expansion part of floating roof tank.
The anti-static and anti-corrosion coating applied in the tank of petroleum products is quite different from other industrial coatings. It must meet two requirements: first, in addition to anti-static, it must have excellent anti rust ability for steel; the inner coating of the tank is immersed in the state of petroleum products, and the immersed state is more conducive to the penetration of corrosive medium through the paint film and corrosion of steel than the atmospheric environment; second, It must be resistant to immersion of petroleum products for a long time, and do not pollute or cause deterioration of petroleum products.
The primer is composed of modified epoxy resin, zinc powder and high-performance curing agent. It is corrosion-resistant based on the principle of sacrificial anode. The iron is not corroded in exchange for the electrons released by zinc powder. The primer has fast drying, excellent impermeability, excellent corrosion-resistant performance and strong adhesion. It is suitable for tank farm environment. The top coat of the scheme is composed of special resin, special pigment and conductive filler, which has excellent antistatic and anticorrosive ability.

The outer wall of fuel tank is in chemical atmospheric environment, and the main corrosion type is primary battery corrosion, which is lighter than that in the tank, but requires outstanding weather resistance. In addition, the environmental temperature of the anti-corrosion oil tank may have an adverse impact on the product. For example, the high temperature in summer is not conducive to the storage of low boiling point oil products, so measures of heat insulation and temperature reduction must be taken to reduce oil loss and ensure production safety.
The recommended anti-corrosion coating scheme for the outer wall of oil tank is: epoxy Iron Red Antirust Primer (brush or spray 2-3 layers, thickness 80-100 μ m) + epoxy micaceous iron intermediate coating (brush or spray 2-3 layers, thickness 100-120 μ m) + tank thermal insulation and anti-corrosion finish (brush or spray 2-3 layers, thickness 80-100 μ m). For the sandblasted surface of pressure vessel, epoxy zinc rich primer (brush or spray 2-3 layers, thickness 80-100 μ m) can be used Degree 80-100 μ m) to enhance the anti-corrosion effect. Epoxy micaceous iron midcoat has a good shielding effect, and can play a lasting protective role in long-term anti-corrosion engineering. The tank insulation coating can reduce the oil temperature (compared with that when the coating is not applied) by 7-10 ℃ in summer and high temperature season, and has excellent weather resistance and anti-corrosion decorative ability, and the paint film is resistant to spray water erosion.
Next article:
Send Your Inquiry
We not only provide a good product, but also provide high quality service. If you are interested in our products,
you can contact us in the following ways.
you can contact us in the following ways.