Product Category
Preliminary inspection of double layer oil tank
Date: Jul 08, 2020

Pay attention to the inspection of the double-layer oil tank in the early stage, so as to ensure the smooth operation of the pressure vessel in the later stage and reduce the occurrence of accidents
1. Tank wall test: Carry out a water filling test on the newly built or repaired oil tank, check whether the double-layer oil tank wall is tight, and conduct an appearance inspection on the oil tank wall plate and the weld.
2. Wall thickness detection: materials entering the market must be inspected into the warehouse. The ground double-layer oil tanks are mainly inspected by ultrasonic waves, which has high efficiency.
3. Welding seam of kerosene tightness inspection: The penetration of kerosene is extremely strong. Welding seam on the wall of the pressure vessel is coated with kerosene for tightness inspection to remove dirt and white powder emulsion. After drying, it is on the other side of the oil tank Spray kerosene on the welding seam. If the kerosene is sprayed after 12 o'clock (the time can be extended when the temperature is low), the surface of the white weld seam has no spots, then the weld seam meets the requirements.
4. Tank bottom detection: The magnetic flux leakage scanning technology detects the corrosion status of the oil tank bottom plate (such as corrosion depth and area, crack length, etc.). The detection principle of this instrument is: the magnetic flux leakage scanner detects the bottom of the oil tank, when the oil tank When the bottom plate is defective, the magnetic field distribution changes and the sensor can detect it. The disadvantage is that some areas will be missed, and the bottom of the tank cannot be fully tested. The bottom of the tank is free of debris and dryness. In addition, helium gas can also be injected into the bottom of the tank to detect leaks at the bottom of the tank.
5. bottom plate welding seam detection, vacuum leak test method for tightness detection bottom plate, apply soapy water to the pressure vessel welding seam, cover the vacuum box for observation, and detect leaks by detecting changes in the volume of oil in the oil tank. Minor leaks are not easy to find. Measure the pressure at the bottom of the tank and calculate the weight of the medium in the tank for leak detection of the oil tank. If the quality continues to decrease, it indicates that a leak has occurred.
6. Add dye to the water in the double-layer oil tank, and test the leak point by water pressure test. In addition, you can also listen to the sound on the wall of the pressure vessel or install an acoustic wave sensor on the tank wall, set up an observation well in the tank area to monitor, and use a dipstick to carry out Oil tank liquid level detection and leak detection, when the oil tank performs sending and receiving operations, it performs leak detection based on the difference between the actual in and out volume.
1. Tank wall test: Carry out a water filling test on the newly built or repaired oil tank, check whether the double-layer oil tank wall is tight, and conduct an appearance inspection on the oil tank wall plate and the weld.
2. Wall thickness detection: materials entering the market must be inspected into the warehouse. The ground double-layer oil tanks are mainly inspected by ultrasonic waves, which has high efficiency.
3. Welding seam of kerosene tightness inspection: The penetration of kerosene is extremely strong. Welding seam on the wall of the pressure vessel is coated with kerosene for tightness inspection to remove dirt and white powder emulsion. After drying, it is on the other side of the oil tank Spray kerosene on the welding seam. If the kerosene is sprayed after 12 o'clock (the time can be extended when the temperature is low), the surface of the white weld seam has no spots, then the weld seam meets the requirements.
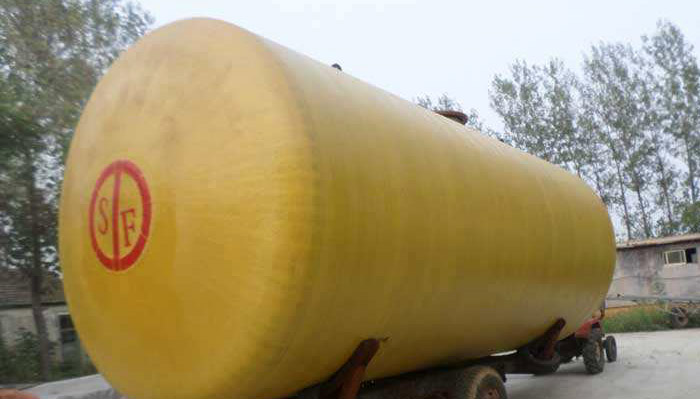
5. bottom plate welding seam detection, vacuum leak test method for tightness detection bottom plate, apply soapy water to the pressure vessel welding seam, cover the vacuum box for observation, and detect leaks by detecting changes in the volume of oil in the oil tank. Minor leaks are not easy to find. Measure the pressure at the bottom of the tank and calculate the weight of the medium in the tank for leak detection of the oil tank. If the quality continues to decrease, it indicates that a leak has occurred.
6. Add dye to the water in the double-layer oil tank, and test the leak point by water pressure test. In addition, you can also listen to the sound on the wall of the pressure vessel or install an acoustic wave sensor on the tank wall, set up an observation well in the tank area to monitor, and use a dipstick to carry out Oil tank liquid level detection and leak detection, when the oil tank performs sending and receiving operations, it performs leak detection based on the difference between the actual in and out volume.
Last article:
Next article:
Send Your Inquiry
We not only provide a good product, but also provide high quality service. If you are interested in our products,
you can contact us in the following ways.
you can contact us in the following ways.